Locking devices for electrical hazards: How and which should I use?
- Posted on
- By Marit Krol
- Posted in circuitbreaker, electrical hazards, lockout devices
- 0
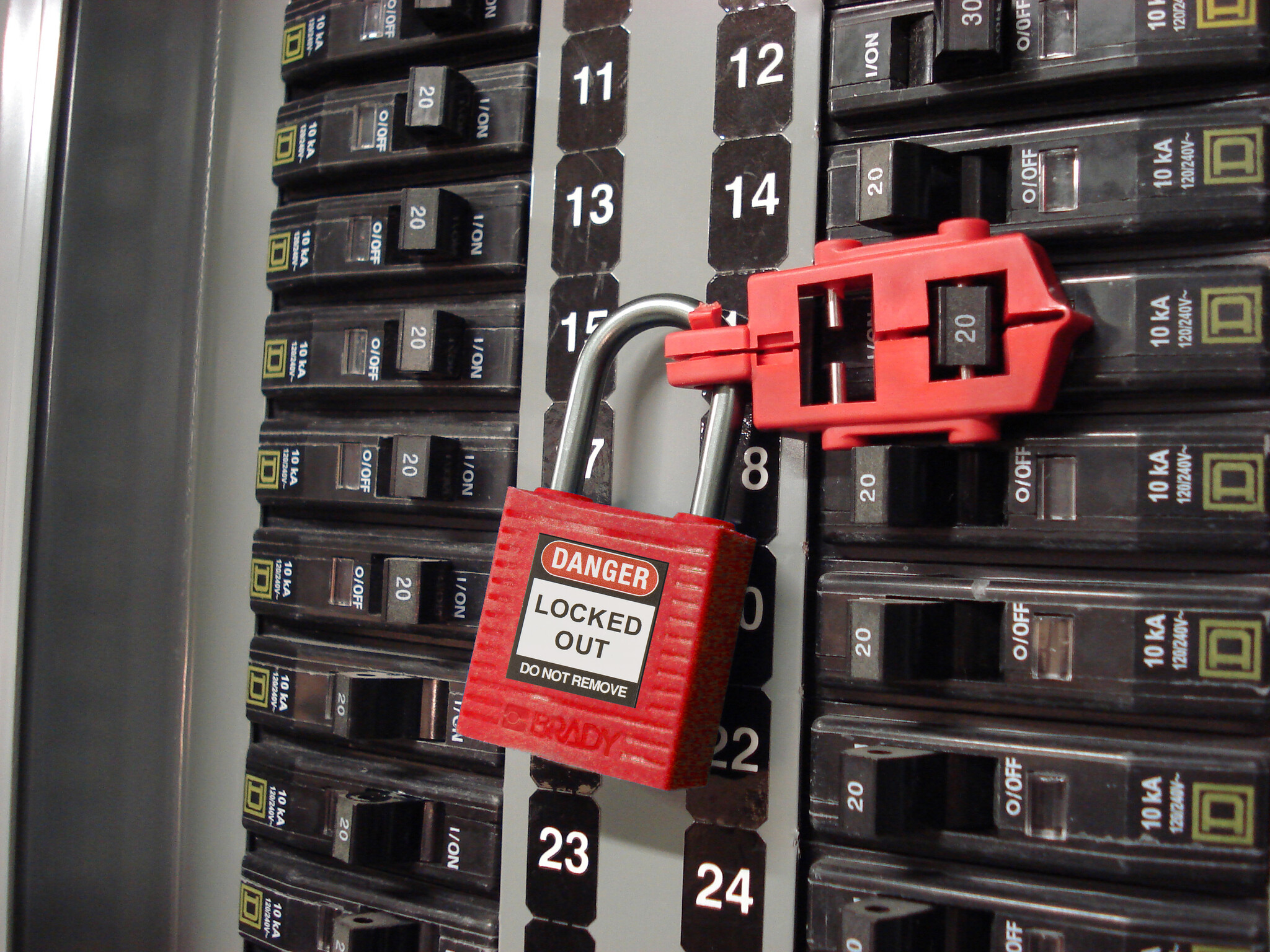
The locking of electrical sources during (maintenance) work is crucial for preventing electrical accidents.
There are a few specific laws and standards governing the safe locking of electrical sources during maintenance. In the US, for instance, the Occupational Safety and Health Administration (OSHA) oversees LOTO procedures under standard 29 CFR 1910.147. Similar regulations exist in Europe, outlined through directives such as the Machinery Directive (2006/42/EC) and the Occupational Health and Safety (OSH) directive (89/391/EEC). These legislations aim to ensure worker safety by enforcing appropriate measures during maintenance activities. For more information on these legislations, read the following article.
Before starting maintenance it is important to identify and locate each electrical source, including switchboards, circuit breakers, electrical panels, and other equipment. This involves a standard procedure of isolating and locking energy sources before maintenance begins. All maintenance staff should receive training in LOTO procedures and use appropriate locking and tagging equipment. Additionally, all energy sources should be safely shut down according to the relevant procedures, such as switching off the main switch or disconnecting power from external sources.
Locking systems for electrical hazards can take various forms, such as padlocks, locking switches, or locking clamps. It is important to use the appropriate type of locking system that is suitable for the specific situation and to ensure that it is safely applied.
Then after applying locks to electrical sources, it's essential to verify that the lockouts are correctly applied and that energy isolation is effective. This can be done through visual inspection or by using checklist procedures.
There are different lockout devices for different electrical hazards. Lockout-Tagout-Shop sells lockout devices for:
Circuit breakers
- Pin-in: These lockout devices are designed to fit into the holes or notches typically found on circuit breakers. By inserting the pin-in lockout device, the circuit breaker cannot be turned on, preventing accidental energization.
- Pin-out: Similar to pin-in lockout devices, pin-out devices also utilize pins but are designed to block the circuit breaker in the "off" position, preventing it from being turned off.
- No pin: Some circuit breakers may not have holes or notches for pin-type lockout devices. In such cases, lockout devices without pins are used. These devices typically encompass the circuit breaker switch, preventing it from being toggled.
- Oversized circuit breakers: For larger or non-standard circuit breakers, lockout devices specifically designed to accommodate their size and shape are used to effectively disable them.
- Motor circuit breakers: Lockout devices for motor circuit breakers are tailored to handle the unique requirements and configurations of circuit breakers used to protect electric motors.
Switches
- Toggle switches: These lockout devices are designed to cover toggle switches, preventing them from being toggled into the "on" position.
- Wall switches: Wall switch lockout devices are designed to cover standard wall-mounted light switches, ensuring they cannot be toggled on.
Fuses
- Screw fuse: Lockout devices for screw-type fuses are designed to cover and secure the fuse holder, preventing the insertion or removal of fuses.
- Blade fuse: Lockout devices for blade fuses are designed to block access to the fuse holder, preventing fuses from being inserted or removed.
- Industrial plugs: Lockout devices for industrial plugs are used to prevent the insertion of plugs into electrical outlets, ensuring that equipment cannot be powered on during maintenance.
Batteries: Battery lockout devices are designed to prevent batteries from being inserted into electrical equipment, effectively cutting off power sources.
Pushbuttons: Lockout devices for pushbuttons are used to cover and immobilize pushbuttons, preventing them from being pressed and activating machinery.
Emergency stop: Lockout devices for emergency stop buttons are designed to cover and secure emergency stop switches, preventing them from being pressed and stopping machinery.
Control consoles: Lockout devices for control consoles are tailored to cover and secure control panels or consoles, preventing access to switches and buttons, thus disabling the control function.
Each type of lockout device serves a specific purpose, ensuring that various electrical components cannot be operated or energized during maintenance or servicing, thus enhancing safety for workers. Check out our full range of lockout devices for electrical hazards here.
Comments
Be the first to comment...