Avoiding Workplace Hazards: Key Mistakes to Avoid When Implementing Lockout Tagout Procedures
- Posted on
- By Marit Krol
- 0
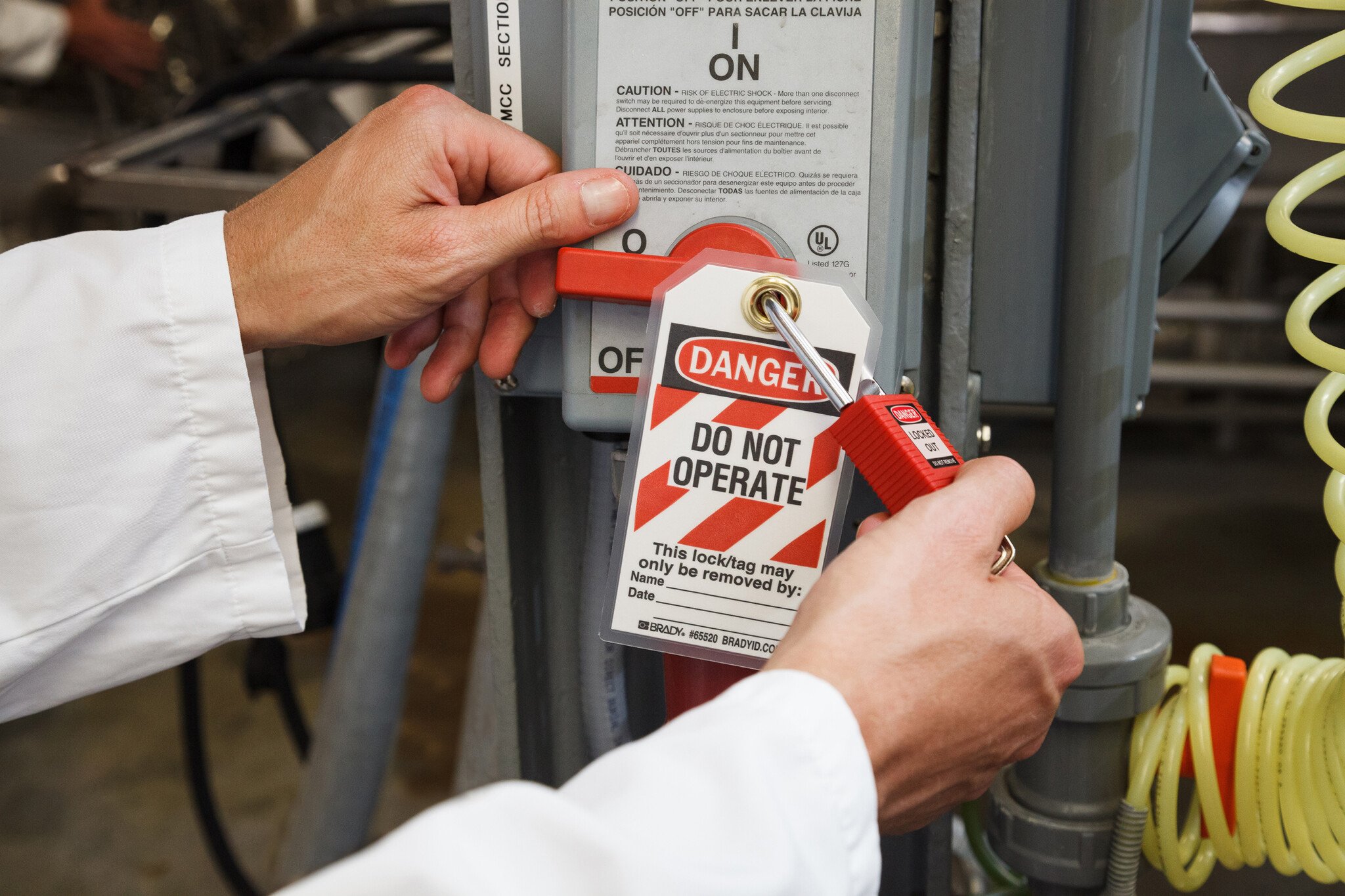
Safety in the workplace is paramount, especially when it comes to hazardous equipment and machinery. One critical safety measure employed in various industries is Lockout Tagout (LOTO), a procedure that safeguards employees by ensuring that machinery and energy sources are properly shut down and prevented from being restarted during maintenance or servicing. However, despite its significance, there are common mistakes that organizations make when implementing LOTO procedures, jeopardizing the safety of their workforce.
- Failing to Train Employees
Empowering employees with the knowledge and expertise needed to execute LOTO procedures accurately fosters a safety-conscious environment. It instills a sense of responsibility among workers, emphasizing the importance of their role in maintaining workplace safety. Additionally, conducting regular evaluations or assessments following training sessions can gauge comprehension levels and identify areas that might require further clarification or reinforcement, ensuring that everyone remains well-equipped and confident in implementing LOTO protocols.
- Not Using the Right Equipment
Using incorrect or substandard lockout devices poses a direct threat to the safety and efficacy of lockout tagout procedures. Machinery often features intricate energy isolation points, necessitating precise lockout devices tailored to fit and secure these specific areas. Opting for inappropriate or low-quality equipment jeopardizes the effectiveness of energy isolation, leaving personnel vulnerable to unexpected releases of hazardous energy. Properly identifying and employing the right lockout devices is indispensable in safeguarding workers and upholding the integrity of the lockout tagout process.
- Not Regularly Inspecting Equipment
Regular wear and tear on equipment is a natural occurrence in any operational setting. However, neglecting routine inspections of lockout devices and safety equipment significantly heightens the risk of malfunction or inefficiency. These crucial safety components are the first line of defense against unexpected energy release. Regular checks, supplemented by proactive maintenance, play an indispensable role in guaranteeing that these safety devices are not only present but fully functional when needed most.
- Not Following the Correct Sequence of Lockout Steps
LOTO procedures involve a specific sequence of steps that must be adhered to for effective isolation of energy sources. Skipping or performing these steps out of order increases the risk of accidents. Proper adherence to the sequence ensures comprehensive shutdown and prevents unexpected energy releases. The correct sequence of Lockout Tagout:
- Step 1: Coordination
The procedure should be discussed in advance with the team. Determine the nature and duration of the work and which equipment needs to be locked out. Communicate the work with the team. - Step 2: Shut off the equipment
Shut down the machine. - Step 3: Isolate
It is not enough to activate an emergency stop device or control circuit. The power source must be completely shut off. Always check for residual energy. - Step 4. Lockout
The locking point that disables the separation of the energy needs to be immobilized with a safety padlock. Never give the key of your personal safety padlock to someone else. - Step 5: Tagout
Locked out equipment should be identified with specific tags to indicate that work is in progress and that the equipment should not be unlocked. - Step 6. Tryout
Check that the device is properly locked out: a start-up attempt, a visual check of the presence of a lockout system or measuring devices indicating the absence of voltage, pressure and flow. - Step 7: Perform the work
When you are certain the machine is correctly locked out you can perform the maintenance and/or cleaning work on the machine.
- Not Following OSHA Standards
The Occupational Safety and Health Administration (OSHA) sets guidelines and standards for LOTO procedures to ensure worker safety. Failure to comply with these standards not only compromises safety but also exposes the organization to legal liabilities and fines. More information on OSHA can be found here.
- Allowing Unauthorized Personnel Access to Restricted Areas
Access control is crucial during LOTO procedures. Allowing unauthorized personnel into areas where lockout procedures are being carried out can lead to accidents. Strict adherence to access control measures is vital to prevent unauthorized entry and potential hazards. Adherence to stringent access control isn't just a procedural necessity but a commitment to the safety culture within a workplace. Instances of unauthorized personnel in lockout tagout zones can disrupt the systematic isolation of energy sources, leading to unforeseen energy releases that can result in severe injuries or fatalities. Continuous monitoring and reinforcement of access protocols are vital to ensuring a safe working environment during maintenance procedures.
- Not Verifying Whether Machines are Turned Off
Assuming a machine is powered down without verifying can be disastrous. A thorough check to confirm that all energy sources are effectively cut off is imperative. Overlooking this step may result in accidental startups, endangering the lives of workers involved in maintenance or servicing. Simply assuming a machine's shutdown status without verification is a gamble no workplace should take. Verifying the cessation of all energy forms, including electrical, mechanical, hydraulic, or pneumatic sources, is indispensable. Disregarding this essential step could trigger unexpected machine movements or unexpected energy releases, placing maintenance personnel at grave risk and jeopardizing the integrity of the lockout tagout procedure.
By steering clear of these common mistakes, organizations can significantly enhance workplace safety, prevent accidents, and create a secure environment for their employees. Regular training, adherence to standards, proper equipment use, and strict compliance with procedures are pivotal in mitigating risks and ensuring the well-being of all individuals involved in handling machinery and hazardous equipment.
Remember, safety is not a choice but a priority! Stay safe and stay informed.
For more information on LOTO procedures, check out our other blogposts!
Comments
Be the first to comment...