Label Printers for Marking Lockout Points and Hazardous Energy Sources
- Posted on
- By Marit Krol
- 0
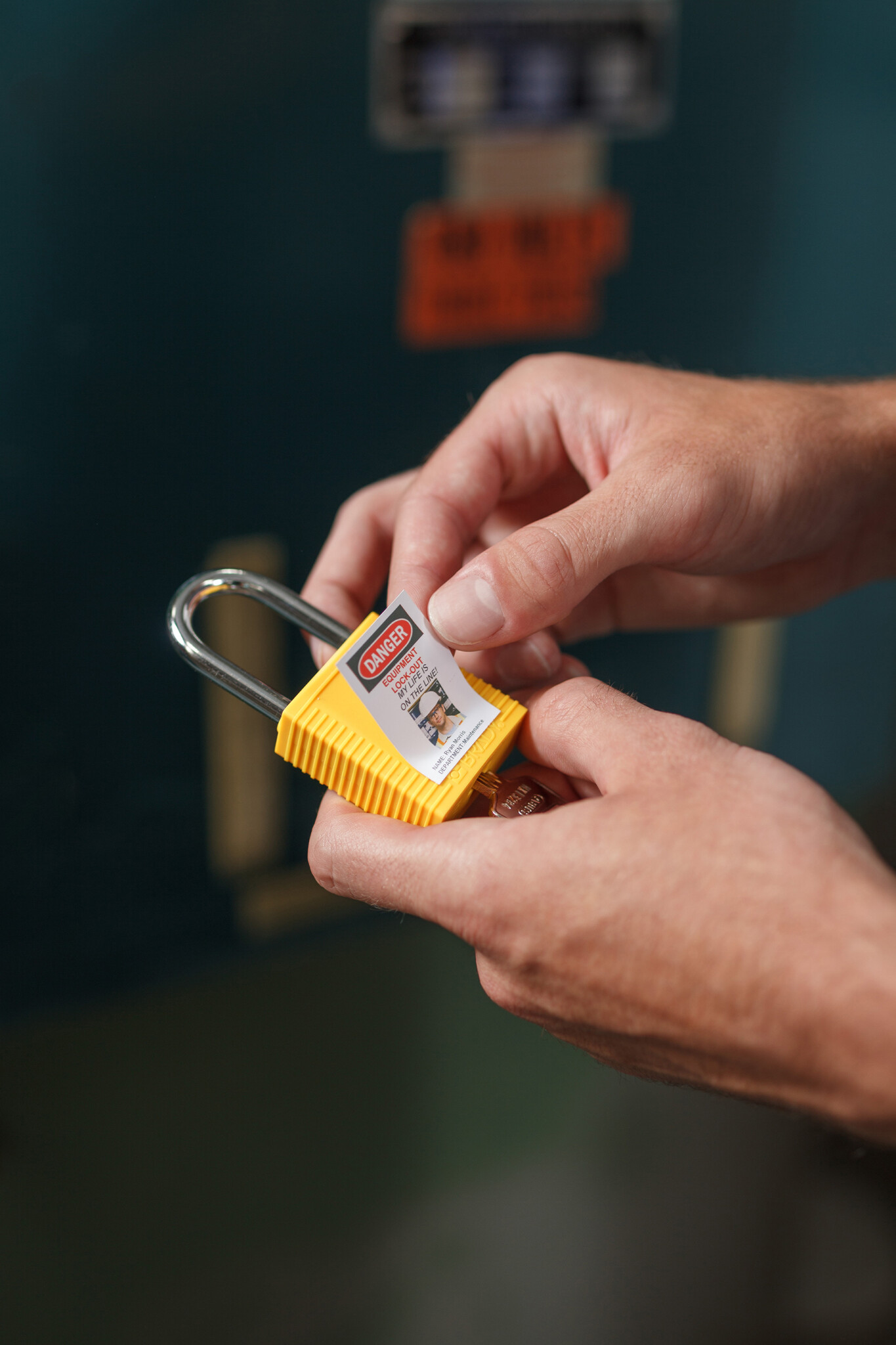
Label printers, essential for marking lockout points and hazardous energy sources, offer a comprehensive solution for identifying and adding necessary information to ensure safety compliance. Brady, our trusted partner, provides a diverse array of label printers tailored to various applications, guaranteeing safety for both employees and management alike.
In contemporary industrial environments, the significance of clearly marked lockout points and energy sources cannot be overstated. Effective labelling serves as a visual aid for workers and plays a pivotal role in adherence to safety regulations and accident prevention. Specifically designed label printers for marking lockout points and energy sources equip organizations with the necessary tools to create standardized, easily recognizable labels that bolster workplace safety. From identifying electrical, mechanical, and pneumatic energy sources to offering precise instructions for lockout procedures, these specialized printers are indispensable for mitigating risks and fostering a secure work environment.
Brady offers an extensive range of label printers tailored to diverse industries and applications, including Datacom, Electrical, Wire and Cable, Laboratory, General Identification, Hazardous Material, Pipe Marking, Rating and Nameplate, Safety, Lean 5S, Inspection, and Repair. Their versatile lineup encompasses portable printers for on-the-go labelling needs, benchtop models for stationary tasks, and robust industrial-grade printers for demanding environments. With over 100 types of ribbons available, Brady ensures a label solution perfectly suited to specific industry requirements. Moreover, Brady's materials are engineered for durability, capable of withstanding extreme temperatures ranging from -70°C to 225°C and resistant to various chemicals and fuels, ensuring longevity and reliability in challenging conditions.
Renowned for their user-friendly design, Brady's label printers prioritize ease of use and maintenance to streamline labelling processes. Featuring intuitive interfaces, operators can swiftly navigate menus and customize labels without extensive training, enhancing productivity and efficiency. Additionally, Brady's printers feature easy-to-load label cartridges, minimizing downtime associated with reloading and ensuring uninterrupted operation. With minimal maintenance requirements, these printers seamlessly integrate into existing safety protocols, minimizing disruptions to workflow. Overall, Brady's commitment to user-centric design ensures that their label printers are accessible and hassle-free, empowering organizations to achieve optimal labelling results effortlessly.
Crucially, Brady's label printers enhance lockout-tagout procedures by providing clear and standardized labels for identifying lockout points and energy sources. These labels serve as visual cues, enabling workers to easily pinpoint hazardous areas and equipment requiring lockout procedures. By utilizing Brady's printers to create standardized labels, organizations maintain consistency across facilities, mitigating the risk of confusion and human error during lockout-tagout procedures. This consistency fosters a safer work environment by ensuring all employees comprehend and adhere to established protocols for isolating energy sources and preventing accidents.
Moreover, Brady's label printers seamlessly integrate with lockout-tagout procedures, enabling organizations to customize labels according to specific needs. Whether identifying electrical, mechanical, or pneumatic energy sources, Brady's printers facilitate the creation of labels with pertinent information, such as equipment identification numbers, lockout instructions, and hazard warnings. This customization ensures labels meet regulatory requirements and effectively communicate critical safety information to workers, enhancing the overall effectiveness of lockout-tagout procedures. With Brady's label printers, organizations streamline lockout-tagout processes, reduce the risk of workplace accidents, and prioritize employee safety.
As labelling technology continues to evolve, exciting developments stand poised to revolutionize workplace safety practices. One notable trend is the integration of RFID (Radio Frequency Identification) tags into labelling systems, enabling real-time tracking and monitoring of assets and equipment. This technology offers enhanced visibility and traceability, enabling organizations to promptly locate items and verify their status, thereby enhancing efficiency and reducing the risk of workplace accidents. Additionally, advancements in digital printing capabilities allow for the production of high-quality, customizable labels with intricate designs and variable data, catering to the diverse needs of modern workplaces. Furthermore, the emergence of cloud-based management systems provides centralized control and accessibility to labelling data, facilitating seamless collaboration and compliance management across distributed work environments. These innovations hold the potential to revolutionize workplace safety practices by enhancing visibility, efficiency, and control over labelling processes, ultimately contributing to a safer and more productive work environment.
Want to explore our range of Brady label printers? Check out our products on https://www.lockout-tagout-shop.com/en/label-printers/
Comments
Be the first to comment...